Achieve Peak Operational Excellence, Drive Safety & Ensure Regulatory Compliance with the #1 Mobile Operator Rounds Solution
An AI-powered platform to ensure compliance and seamless operations, 24/7.
mRounds automates routine inspections, shift handovers, audits, and regulatory compliance, helping you stay audit-ready and incident-free.

Trusted by Operators and Frontline Workers Worldwide
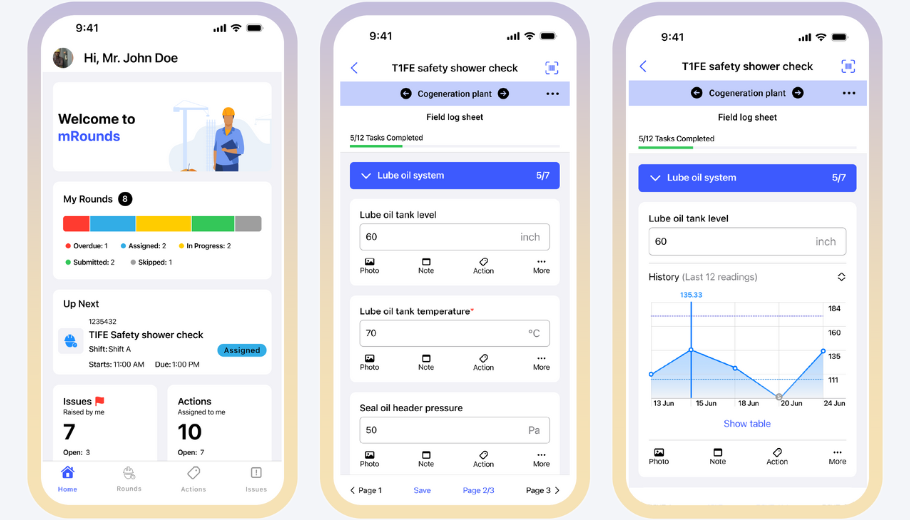
Ensure Operators Love Every Round - Fastest & Easiest Experience
Mobile Operator Round
- Best-in-class User Experience: Utilize a modern, easy-to-use interface
- Unbeatable Offline Experience: Powered by our proprietary RapidSync™.
- Access Historical Data: Instantly retrieve past round data and process info for smarter decisions.
- Versatile Data Capture: Collect all types of data with 18+ response options, including photos, videos, and audio.
- Mobile Handover: Ensure smooth transitions with mobile handover reports, contextual chat, and multimedia support.
Digitize Your Inspection Rounds in a Flash!
Inspection Rounds & Route builder
- Instantly Convert with AI/ML: Transform thousands of inspection rounds using AI/ML and OCR scanning.
- No-Code Authoring: Create new inspection forms effortlessly with a simple drag-and-drop interface.
- Mobile Preview While Authoring: Visualize and test your rounds in real-time on any mobile device.
- Template Library: Access predefined templates tailored for your industry-specific inspections.
- Advanced Scheduler Engine:Intuitive visual platform for optimized shift and slot-based round scheduling, enabling flexible role and position assignments.
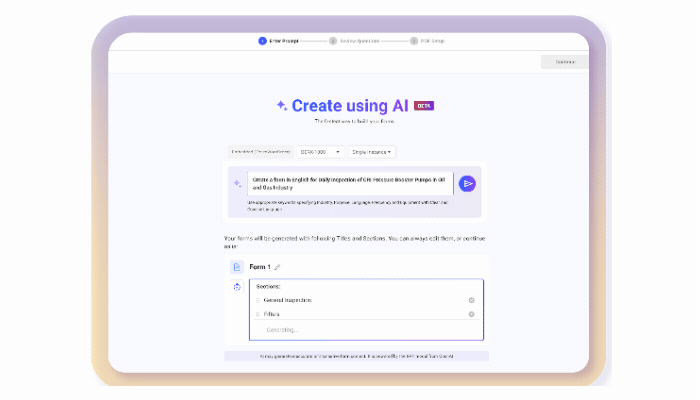
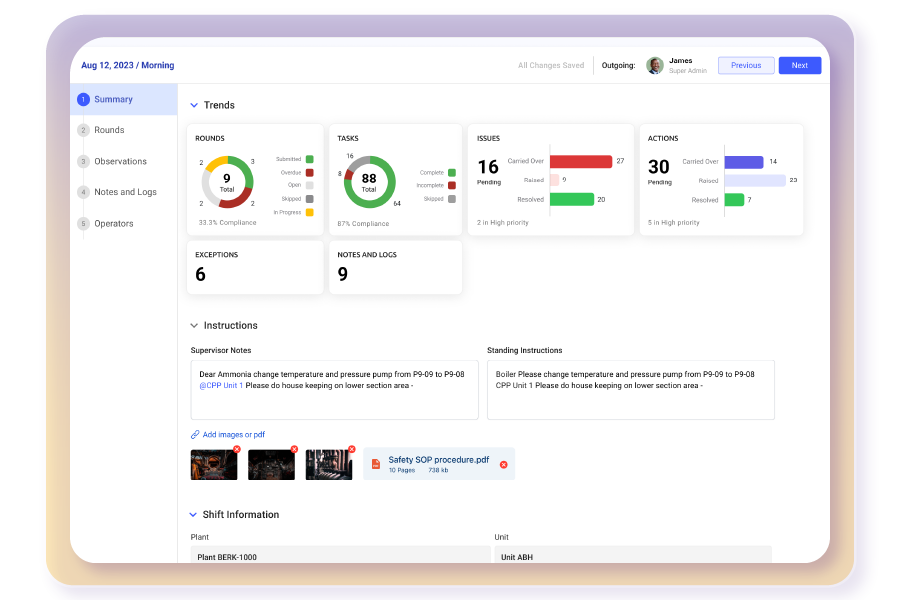
Seamless Shift Handovers – Maintain Continuity
Integrated Shift Turnover
- Industry’s First Automated Handover Report: No manual transitions required with our fully automated shift handover reports.
- Effortless Shift Handover: Operators can easily pass on critical information, including ongoing tasks, completed rounds, observations, and outstanding issues to the incoming shift.
- Exception Reporting: Anomalies or out-of-spec conditions are automatically reported in shift turnover reports.
- Position-Level Handover: Operator-to-Operator, Operator-to-Supervisor, and Supervisor-to-Supervisor with approvals.
Streamline Issue Reporting for Immediate Action
Work Notification Entry
- Quick ERP Notification Entry: Operators can swiftly log work notifications directly into ERP systems from the field.
- Instant Issue Reporting: Log ERP (SAP, Maximo, Oracle, etc.) maintenance requests, equipment malfunctions, or safety hazards instantly, triggering immediate action.
- Track Issues in Real-Time: Monitor and manage issues and actions in the back office with real-time updates.
- Chat Collaboration: Ensure prompt communication and prevent potential disruptions.
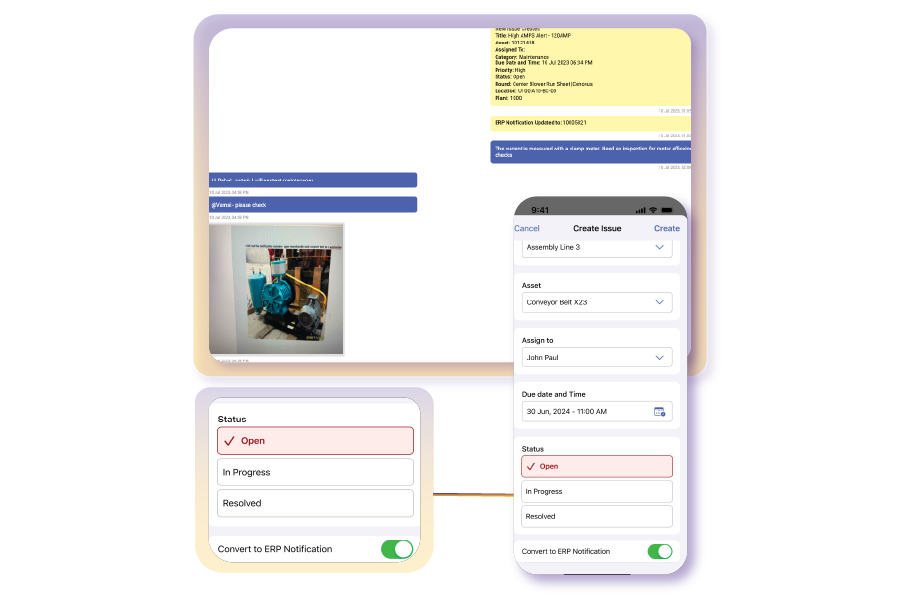
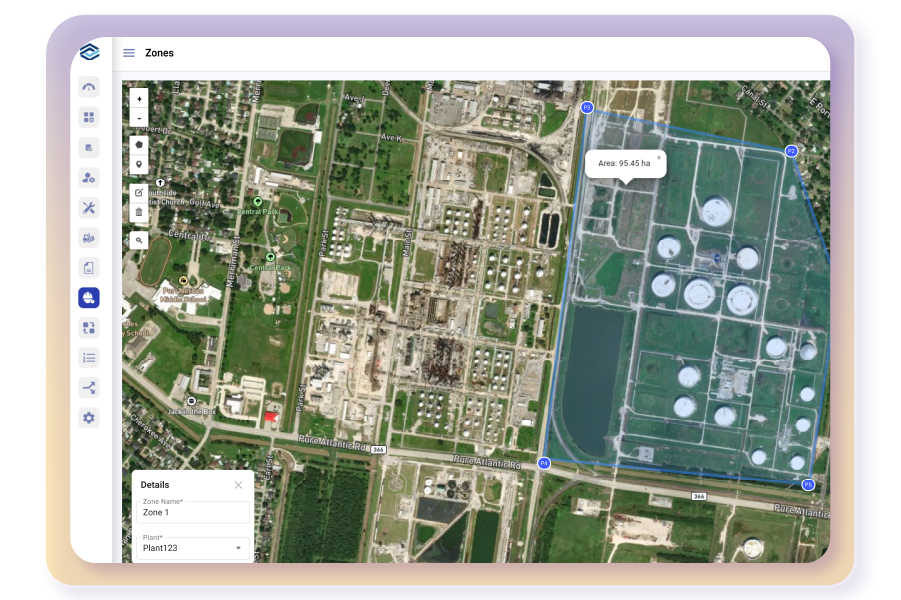
Maximize Worker Productivity with Location Intelligence
Identify Production Zones of Operators
- Exclusive Monitoring Solution: The ONLY operator round solution for tracking data entry points throughout the facility.
- 100% Productivity Insights: Ensure operators remain fully productive with real-time data.
- Real-Time Zone Identification: Define and monitor operator zones to maintain seamless operations.
Enhance Quality Control with AI-Driven Image Analysis
Computer Vision for Issue Identification
- Direct MTBF Impact: Improve Mean Time Between Failures with precise defect detection.
- AI/ML Image Analysis: Harness AI and machine learning to identify issues that may be missed by the human eye.
- Actionable Insights: Receive recommended actions based on real-time image analysis.
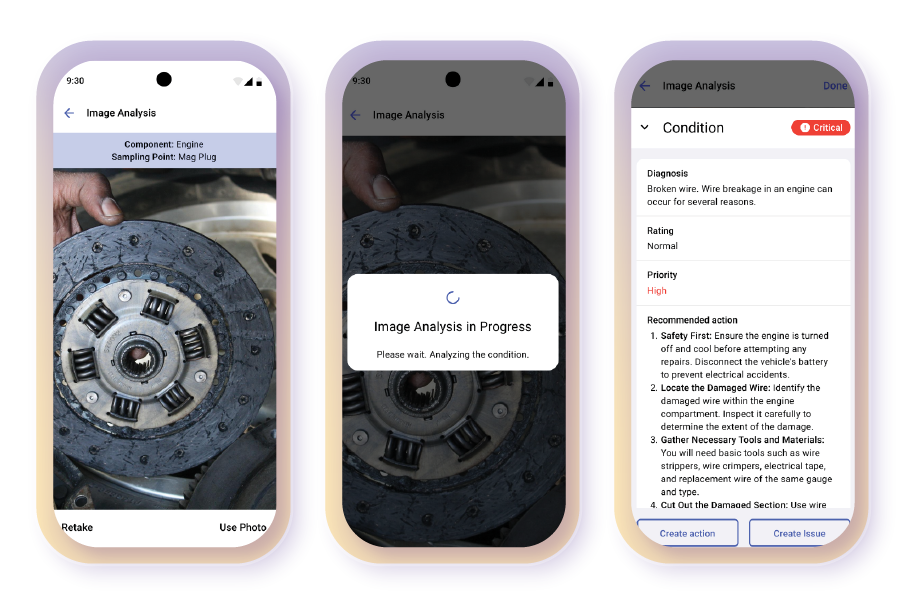
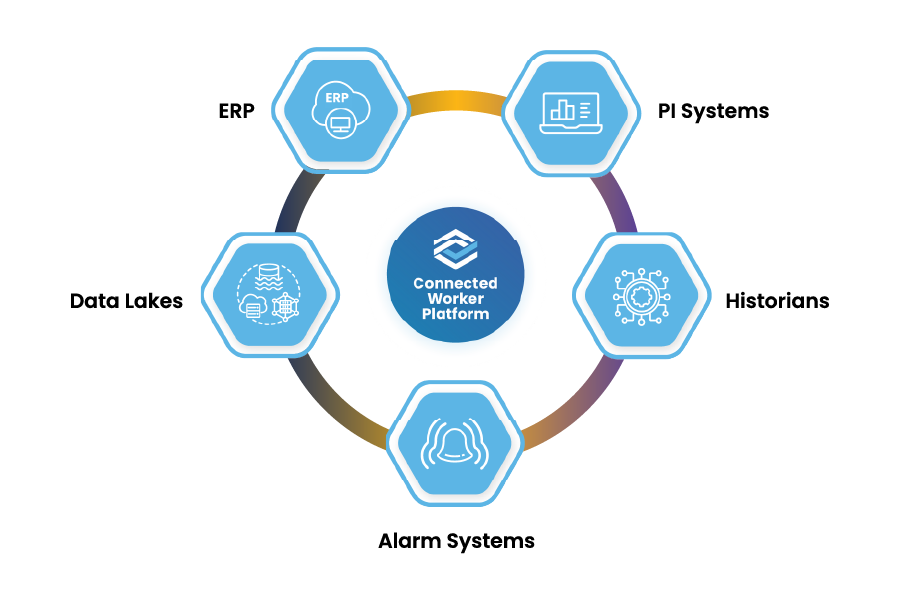
SIngle-Pane-of-Glass
Integration
- Proven Process Information Integration: Seamlessly connect with leading process information systems.
- APM Solutions Integration: Ensure compatibility with top APM solutions.
- EAM/CMMS/MES Integrations: Rapid deployment in your facility.
- API-Based Integration: Utilize API integration for flexible and efficient data exchange.
- OPC HDA-Based Integration: Leverage OPC HDA for robust and reliable data integration.
Assess Risks with Smart, Heatmap-Based Automation
Risk Prioritization Matrix
- Heatmap-Based Prioritization: Quickly identify and prioritize risks using an intuitive heatmap system.
- Reduce Manual Errors: Minimize human error in risk assessments with automated, data-driven processes.
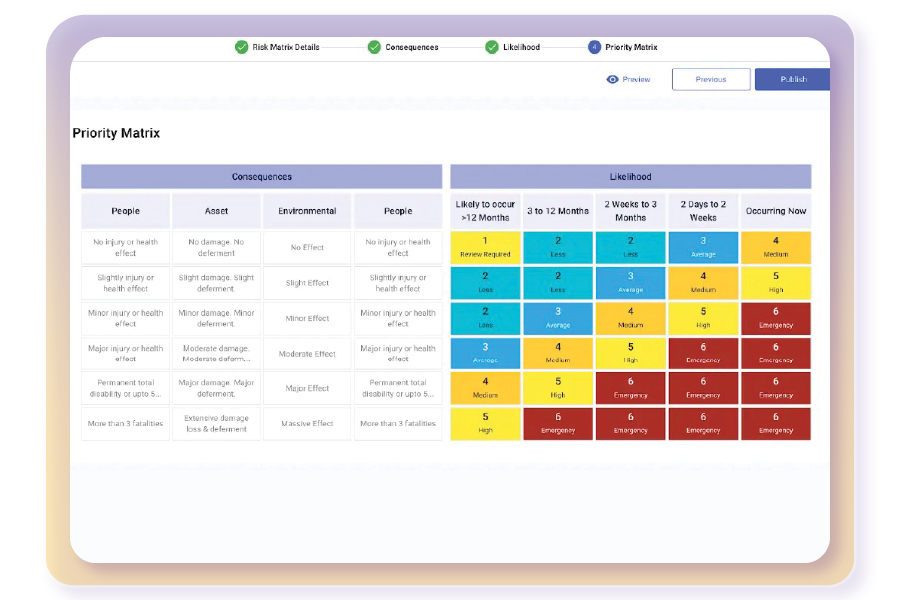
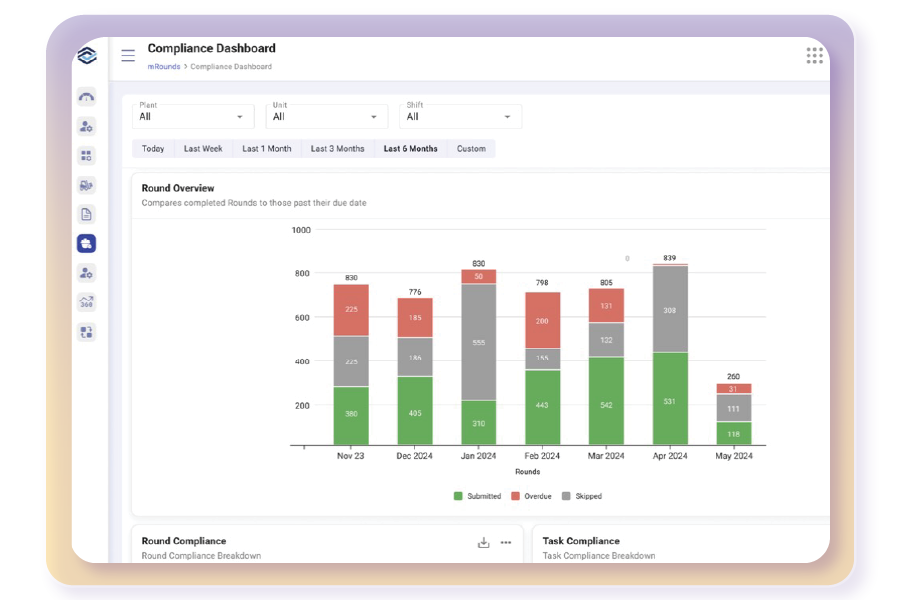
Leverage AI for Predictive Insights and Compliance Tracking
AI/ML-Based Data Analytics
- AI-Powered Predictive Analysis: Use an AI agent for advanced predictive analytics to stay ahead of potential issues.
- Pre-Configured Dashboards: Track compliance effortlessly with pre-built dashboards and reports.
- Configurable KPIs: Monitor and analyze critical metrics like MTTR and MTBF, tailored to your needs.
Simplify Approvals with Signatures
Approval Workflow Wizard
- Streamlined Approval Processes: Simplify approvals with drag-and-drop capabilities.
- Efficient Task Tracking: Monitor and manage tasks seamlessly with Innovapptive’s intuitive workflow management.
- Integrated Rounds and Permits: Combine rounds approval, permits, and MOCs into a single, cohesive workflow.
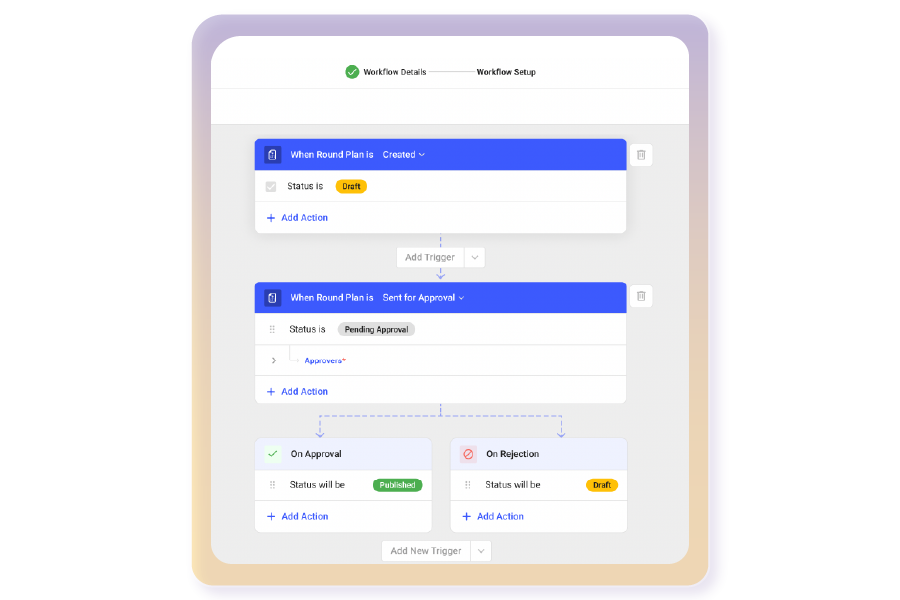
Why Innovapptive For Your Mobile Rounds
Digitize Rounds Planning
Create detailed operator rounds plans, assignments, and routes – no paper involved.
View What the Round Looks Like Before Issuing
See round plans as they will look to the operator in the field.
Import Fields from
Previous Rounds
Save authoring time by reusing tasks and questions.
Customize Responses
Tailor questions and answers to ensure rounds are completed correctly and accurately.
Configure Units of Measure
Set measurements to conform to specific location requirements.
Establish Measurement
Limit Alerts
Sending an automatic notification when a measurement exceeds a pre-set limit.
Set Up Mandatory Fields
Ensure fields can’t be skipped and must be entered before a round can end.
Require Evidence and Justification
Add logics so that an operator must include attachments or photos.
Create a Digital System
of Records
Produce a customized, comprehensive report to share with stakeholders.
Gain Speed and
Agility in Responses
View pictures and notes; issue notifications, and make assignments in real time.
Follow-up
Roadmap Reduces Risks
Create notifications and reminders for any completed task.
No Internet Connection?
No Problem
Complete tasks offline, then rapidly sync the application when connectivity is re-established.
A Flexible, Agile, and Totally Digital Operator Rounds Process
- Plan, schedule, and issue a round from anywhere at any time
- Configure a digital form to meet the company’s business needs or new regulations in less than 30 minutes
- Avoid the need for coding or technical knowledge and get productive from the get-go
Is mRounds the Right Solution for You?
Innovapptive serves industries like oil and gas, chemicals, utilities, mining, and manufacturing. Here is how your organization can leverage mobile operator rounds.
Oil and Gas
- Use at any oil and gas facility, either onshore or offshore: an upstream drilling site, a midstream processing plant or pipeline, or a downstream refinery
- Identify potential equipment issues in the early stages
- Take proactive action before they contribute to costly incidents
- Ensure production assets remain up and running and workers remain safe
Chemicals
- Use at any chemical processing facility, including giant petrochemical plants, agricultural chemicals factories, or process chemical plants.
- Accurately monitor asset health in real time
- Gain valuable early warning to potential issues
- Ensure production assets remain up and running and workers remain safe
Mining
- Use in open-pit, surface, subsurface, or in-situ mines
- Spot areas of concern regarding equipment condition or safety
- Take prompt action to resolve the situation before an incident occurs
- Ensure production assets remain up and running and workers remain safe
Utilities
- For use in electric generation, power transmission, natural gas distribution, or water/wastewater facilities
- Gain greater operational visibility into current conditions
- Take fast remedial action when a potential issue is spotted
- Reduce equipment downtime incidents and promote a safer workplace
Manufacturing
- Use in any manufacturing plant: assembly, casting, forging, stamping – from automobiles and machinery to durable goods and consumer products
- Understand current operating and reliability conditions in real time
- Take appropriate actions an issue causes downtime or a safety problem
- Ensure production assets remain up and running and workers remain safe