Reduce Asset Downtime with Increased Efficiency and Productivity
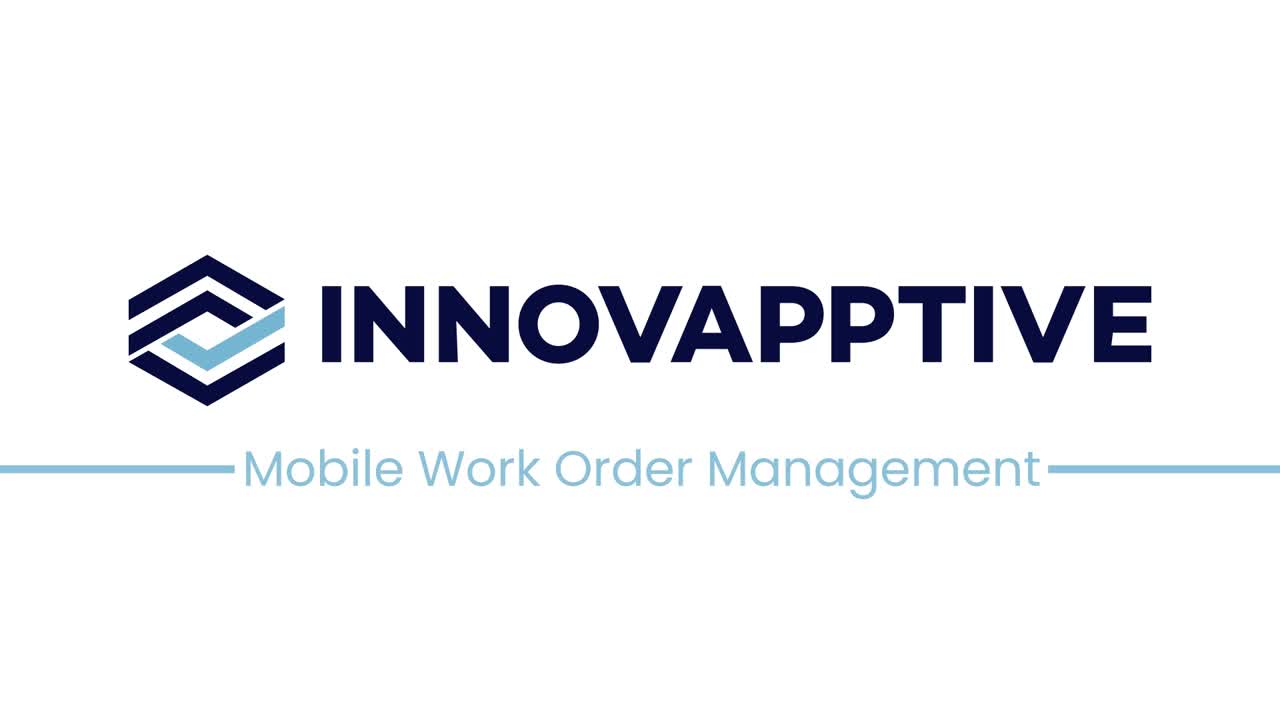
Mobile Maintenance Solution Trusted by 5,000+ Frontline Workers Worldwide
Asset-intensive companies love Innovapptive
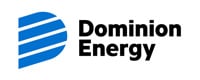
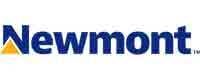
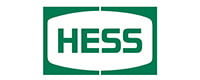
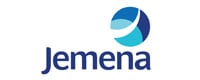
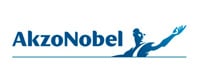
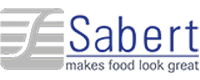
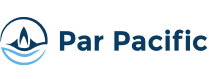
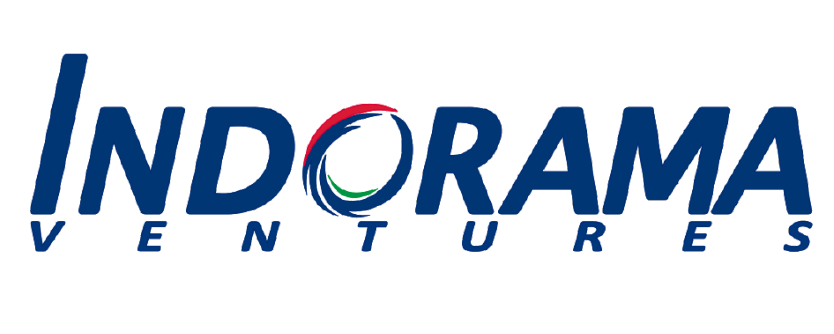
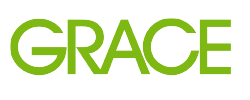
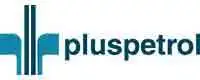
Go from Reactive to Proactive Maintenance
Work order management teams are plagued with administrative inefficiencies, low levels of visibility, and limited collaboration with field technicians. As executives, we expect to see high-functioning facilities, but without automation and mobilization technologies, work order managers are hard-pressed to deliver.
Work Order Management solution from Innovapptive comprising of mobile app mWorkOrder and Control Centers suit are designed to improve planning accuracy, reduce delays and wasted productivity, enable real time work queue management and prioritization, ensure better coordination and visibility, onboard and upskill technicians faster.
- Foster smarter collaboration across operations, maintenance and store room on a single unified platform with connected workflows
- Easily redefine and customize your workflow with our patented rapid app configuration engine technology
- Embed work instructions for the assigned jobs to provide in context, personalized guidance to technicians
- Create and embed dynamic, rule based checklists within minutes with our AI powered capabilities
- Get unified and real-time view of Maintenance Activities with a Kanban style Maintenance and Parts Control Center Suit
- Analyze trends and implement proactive maintenance to ensure safety and compliance across the enterprise
Drive Results with Key Features and Functionalities
-
Asset Equipment Dashboard
Empower technicians with important machine and equipment data.
-
Auto Time Capture
Accurately measure wrench time by automatically capturing time spent on each work order.
-
View Functional Location and Equipment Hierarchy
Drill down from a functional location into an Equipment Hierarchy and locate a specific Bill of Materials (BOM).
-
Capture and Annotate Images, Videos and PDFs
Easily annotate documents and images attached to Work Orders, Notifications, Equipment, Functional Locations and more.
Asset Equipment Dashboard
Empower technicians with important machine and equipment data.
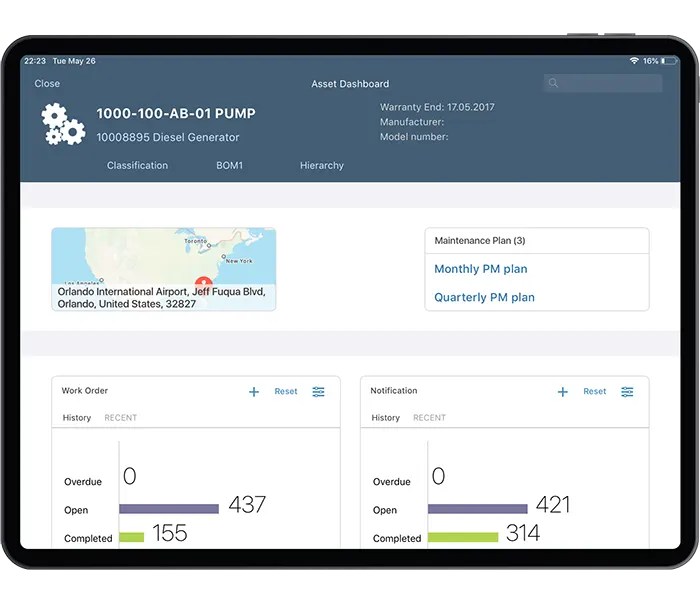
Auto Time Capture
Accurately measure wrench time by automatically capturing time spent on each work order.
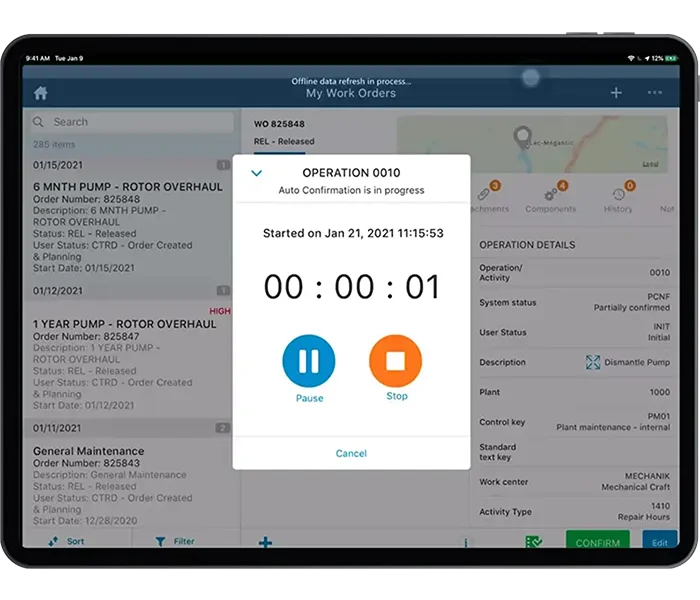
View Functional Location and Equipment Hierarchy
Drill down from a functional location into an Equipment Hierarchy and locate a specific Bill of Materials (BOM).
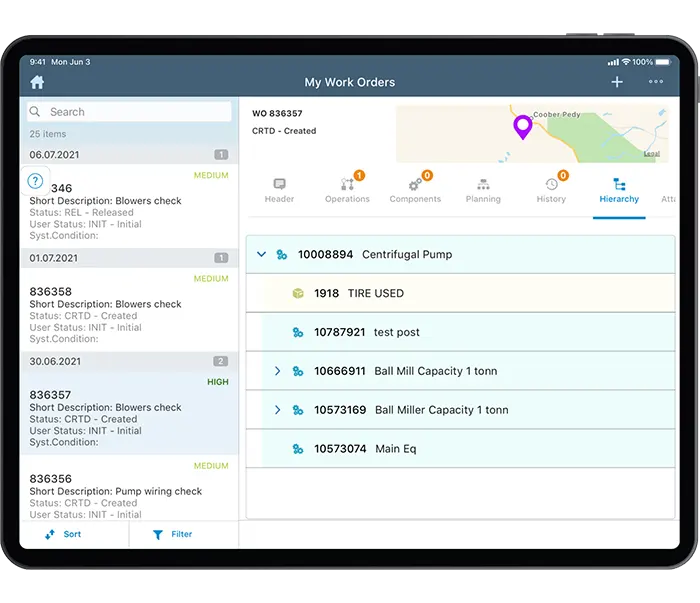
Capture and Annotate Images, Videos and PDFs
Easily annotate documents and images attached to Work Orders, Notifications, Equipment, Functional Locations and more.
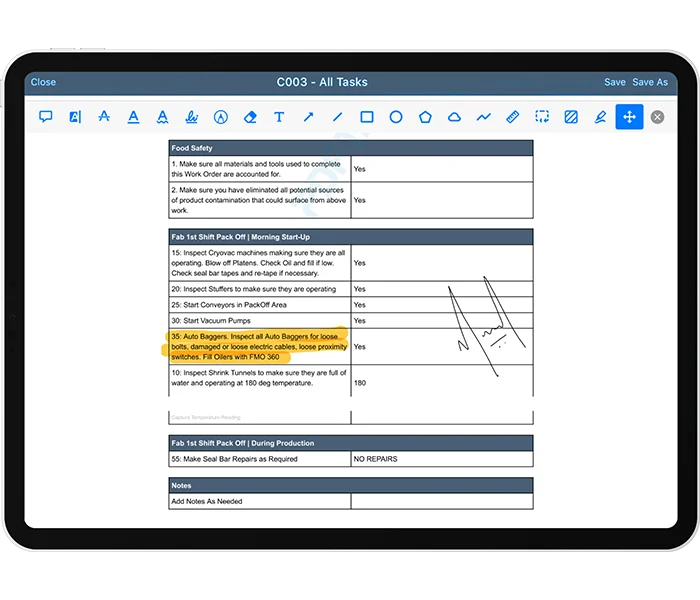
What Innovapptive Delivers
20%
Greater Wrench Time
Technicians spend more time doing what they do best - turning wrenches and repairing equipment.
50%
Reduce Work Backlog
Eliminating paper processes and time spent entering data manually.
80%
Reduce Preventable Failures
Identify and fix problematic equipment before it breaks down.
26%
Lower Maintenance Costs
More accurate and timely data reduces maintenance spend.
Frequently Asked Questions
SAP Mobile Work Order Management simplifies work order creation, scheduling, and tracking, enabling real-time asset monitoring, predictive maintenance, and mobile workforce management. It helps reduce downtime, increase equipment reliability, and streamline maintenance workflows.
Integrating mobile work order management software with SAP EAM, SAP PM, and IBM Maximo allows organizations to digitize maintenance processes, optimize field service management, and improve asset lifecycle performance using connected worker technology.
Work order automation eliminates manual paperwork, reduces maintenance backlog, and ensures faster issue resolution. By leveraging IoT-enabled maintenance and AI-powered scheduling, businesses can optimize work order execution and resource allocation.
Real-time work order tracking provides instant updates on task status, technician availability, and asset performance, ensuring faster response times, predictive maintenance execution, and proactive issue resolution.
Manufacturing, oil & gas, utilities and mining industries leverage SAP-integrated mobile work order management to enhance field operations, improve maintenance scheduling, and enable paperless digital transformation.
Mobile work order solutions support real-time condition monitoring, IoT-enabled predictive maintenance, and AI-driven failure detection to reduce mean time to repair (MTTR) and increase mean time between failures (MTBF).
Field service management software enables technicians to access digital work instructions, complete tasks using a mobile app, and update work orders remotely, improving operator efficiency and maintenance execution accuracy.
SAP mobile work order solutions offer operator compliance tracking, shift log software, safety rounds management, and digital logbooks to ensure audit-ready maintenance execution and regulatory compliance.
The must-have features of a mobile work order management solution are as follows
✔ Mobile work order automation for faster task execution
✔ Preventive maintenance tools to reduce asset downtime
✔ Digital work instructions for step-by-step task guidance
✔ Field data collection tools for accurate asset performance tracking
To implement SAP-integrated mobile work order management, organizations should:
1️⃣ Integrate mobile work order solutions with SAP EAM, IBM Maximo, or SAP PM
2️⃣ Digitize preventive maintenance workflows using AI-powered automation
3️⃣ Enable real-time monitoring with IoT and AI-driven condition-based maintenance
4️⃣ Train maintenance teams on connected worker platforms and mobile asset management best practices
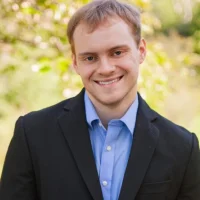
The ease of adding pictures, attachments, and videos to the work order makes it that much more efficient. When we would get them under the old process, they’d be passed around separately through emails and such. Now it’s ‘Here’s a work order and everything associated with it.’ The pipeline converges into SAP and that one work order has everything you need.
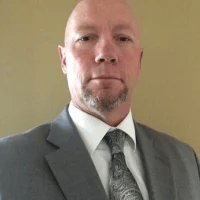
We hadn’t had much luck with mobile plant maintenance solutions in the past. Our frontline maintenance technicians didn’t want to use them because of poor UI/UX. They’d rather use paper, meaning we received a poor return on investment and achieved none of our operational objectives.
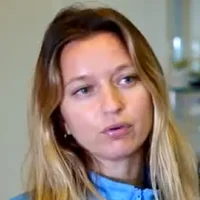
We wanted to make our workers more autonomous, independent, and proactive. We wanted to give them data at their fingertips. With Innovapptive’s mobile maintenance solution, they’ll get that.
Talk with a solution expert today
Resources
Frequently asked questions
Aenean lacinia bibendum nulla sed consectetur. Etiam porta sem malesuada magna mollis euismod. Fusce dapibus, tellus ac cursus commodo, tortor mauris condimentum nibh, ut fermentum massa justo sit amet risus. Curabitur blandit tempus porttitor. Cum sociis natoque penatibus et.
Aenean lacinia bibendum nulla sed consectetur. Etiam porta sem malesuada magna mollis euismod. Fusce dapibus, tellus ac cursus commodo, tortor mauris condimentum nibh, ut fermentum massa justo sit amet risus. Curabitur blandit tempus porttitor. Cum sociis natoque penatibus et.
Aenean lacinia bibendum nulla sed consectetur. Etiam porta sem malesuada magna mollis euismod. Fusce dapibus, tellus ac cursus commodo, tortor mauris condimentum nibh, ut fermentum massa justo sit amet risus. Curabitur blandit tempus porttitor. Cum sociis natoque penatibus et.